Many American construction firms are failing to implement obvious and inexpensive safety measures that could save lives, reduce injuries and avoid costly insurance claims. And many insurers are not nudging their insured contractors to be proactive and preventive.
“It’s usually not until after the fact, after something happens,” said TJ Lyons, a safety consultant who spoke Tuesday at the International Risk Management Institute’s 43rd Annual Construction Risk Conference in Orlando.
A number of property/casualty insurance carriers, such as Crum & Forster, provide safety analysis programs that can lead to considerable premium discounts on auto fleet liability coverage. And contractor-controlled insurance packages can be structured to produce premium discounts when fewer claims are filed. But to a large degree, workers compensation and commercial liability insurers leave it mostly to contractors to vet their operations for safety, experts at the IRMI conference said.
“It takes time to analyze all of that,” said Jes Alexander, a senior research analyst for IRMI. “And there’s sometimes a disconnect between underwriting and claims.”
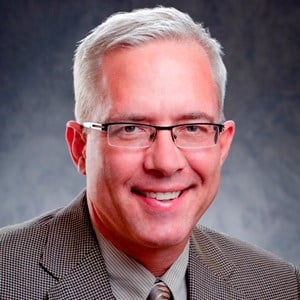
With or without prompting by insurers, commercial construction companies across the country are overlooking crucial changes, many of which have been adopted by European firms, Lyons said. Unsafe practices in the U.S. contribute to some 2,000 construction worker fatalities each year, a rate that is nine times that of Great Britain’s construction industry, said Lyons, a certified safety professional and head of Lyonetics Safety.
The best ways to foster safer worksites is to require best practices and safer equipment as part of the contracts with builders and subcontractors, and to build safety innovations into a project at the design stage, he argued.
“Safety folks are very rarely involved in the design,” Lyons said.
He outlined numerous products and practices that US construction firms have not widely adopted:
Get rid of ladders on construction sites. Falls from ladders are a leading cause of serious injuries and injury claims. Instead, contracts should require that only mechanized lifts be used. Some are now designed to be the right size to lift an electrician, for example, through a ceiling tile gridwork to reach cables above. Stilts, already outlawed in some states, also should be banned because of the injury risk from falls, Lyons said.
Avoid heavy equipment with blind spots. Some cranes and boom trucks have the lift arm at a resting position to the side of the driver compartment, blocking the lateral view. Lyons told the story of an 82-year-old construction manager who had been in construction for decades, only to be killed because the boom-truck driver could not see him.
Utilize safer electrical panels that readily show if the panel is energized, instead of requiring a worker to open the panel to check. Some utilize windows on the panel. Light-up devices also are available.
Don’t use powder-activated fastener systems that contain lead. One popular system, which drives fasteners into concrete with an explosive charge, produces lead dust, Lyons said. But those same guns are available without lead.
“Put it in the contract – guns with no lead,” he added.
Request steel framing studs with rolled edges. Instead of requiring workers to use gloves or letting them get lacerated on sharp steel edges, a better approach is to spend a little more and order rolled-edge framing members or duct work.
“With the diminishing workforce we have now, this is important,” he noted.
Employ drop-arrest hoisting systems. Instead of using a rope to lift heavy loads to height (a method utilized for hundreds of years), drop-stop load arrestors prevent material and equipment from falling onto workers if the rope is released. Such devices are widely used on European jobsites but not in America, Lyons noted.
Have systems pre-assembled and delivered to the project when possible. Electricians can spend hours, with potentially dangerous reel systems to force wire through conduits in a building under construction. And concrete workers may work in heat or cold to tie reinforcing rods together. A better approach is to load the electrical cables into the conduit off-site and to build re-bar mats in the shop. These techniques can also save time, Lyons said.
Install anti-skid pads on stairs and everywhere floors may be slippery.
Hold people accountable. In parts of Europe, Lyons said, supervisors who fail to require the use of safety equipment can be prosecuted.
Require table saws that automatically shut off when the blade comes into contact with skin. One manufacturer, SawStop, has been making the type of saw for years, but most U.S. job sites still don’t require them.
Don’t forget about mental health of workers and supervisors. Some 5,000 U.S. workers take their own lives each year, he said. Construction companies need wellness and suicide prevention programs.
While some insurance carriers may take a hands-off approach to work safety, that doesn’t mean construction insurance can’t be profitable. A number of major construction firms have found that contractor-controlled insurance packages (CCIPs) or owner-controlled packages (OCIPs), which cover almost everything and everyone on a site, can be a big source of profit, experts said at the IRMI conference, which held a session on wrap-up insurance for construction.
The coverage can be structured to be loss-sensitive, with fewer claims producing lower premiums.